SOLID CARBIDE DRILL MANUFACTURERS
“Efficient Services to Enhance Your Productivity We understand the importance of time to your business. By optimizing processes and providing efficient services, we help clients maximize productivity in the shortest possible time. Our team ensures timely project delivery, allowing you to focus on your core business. “
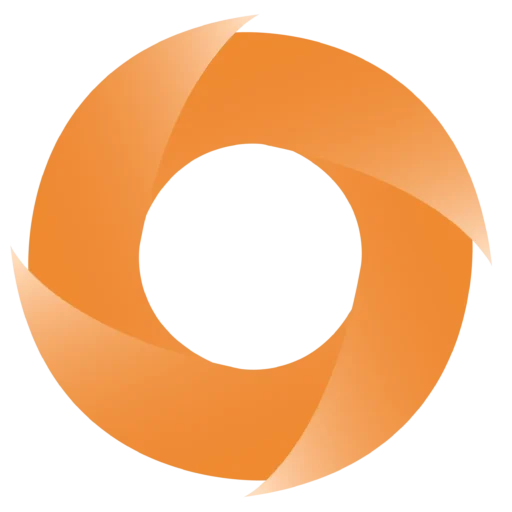
JINOO 精诺
Solid carbide twist drills are cutting tools designed to create precise round holes in workpieces.
Solid carbide spiral drill bits feature a compact design with a helical cutting edge that helps distribute cutting forces, reducing stress on the workpiece and extending tool life. Their advanced design and cutting geometry ensure a smoother drilling process, allowing for precise, round holes in the material.
Carbide Drill Bits Production Process
Carbide drill bits, made from tungsten carbide, which could offer an optimal balance of precision and penetration for drilling tasks.
● Optimized flute design balances cutting edge lightness, tool rigidity, and chip clearance.
● Advanced coating treatment ensures low-resistance, high-efficiency machining.
● Made from high-quality tungsten carbide with a DIN6535HA fixed shank, offering consistent shank diameter across specifications, reducing drill chuck costs.
Drilling Parameters
Drills come in different diameters for different hole sizes and depths.
Smaller diameter drills are commonly used and come in various lengths such as 3D, 5D, and 8D. Features include wide chip flutes for better chip evacuation and corrugated blades for efficient chip breaking.
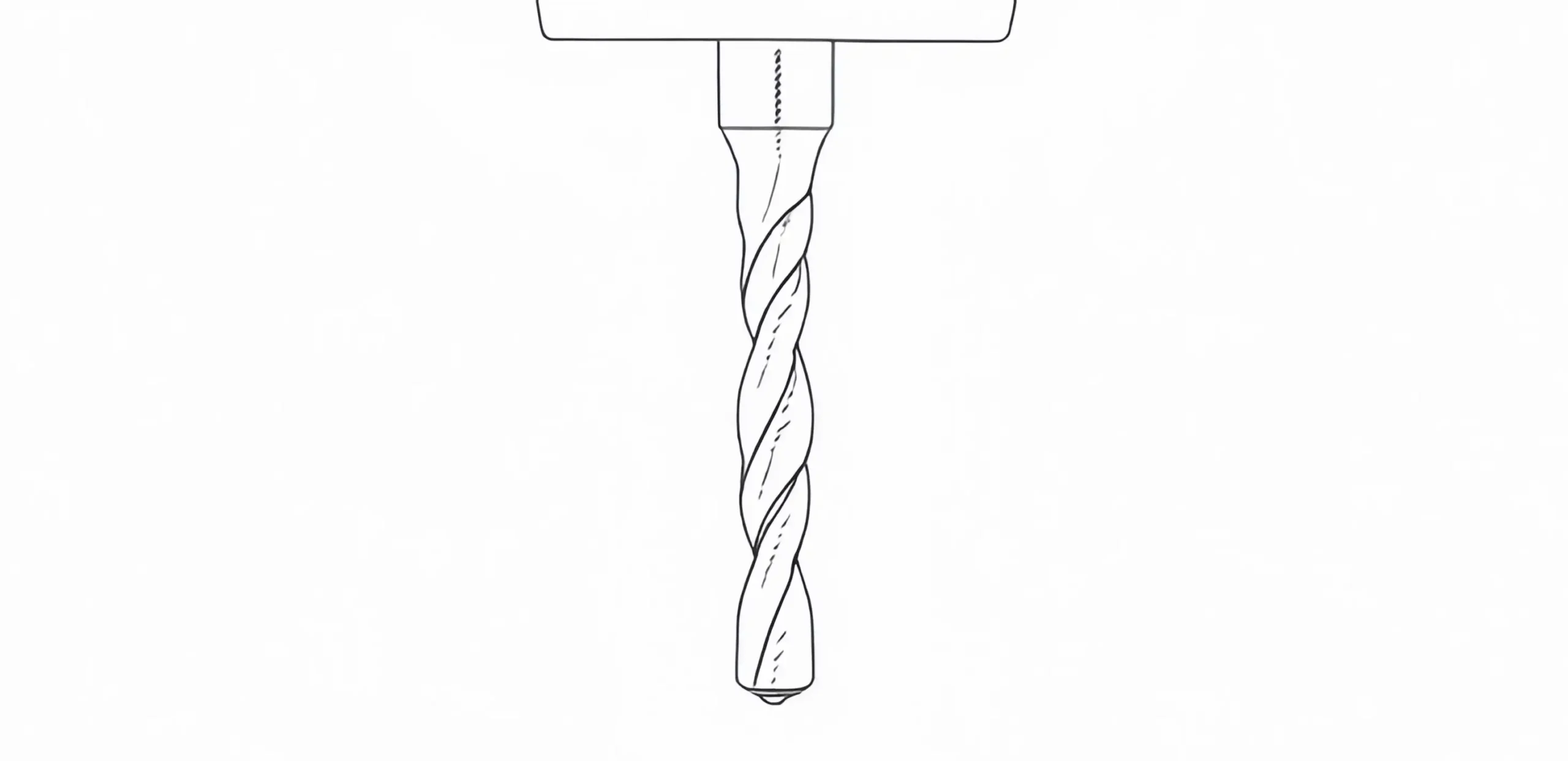
- Small Carbide Drill Bits-Diameter 1-2.9mm
Carbide drill bits with diameters of 1mm to 2.9mm are precision tools designed for accurate small-hole drilling. Made from high-quality carbide, they offer excellent hardness, wear resistance, and durability.
- Micro Carbide Drill Bits 3D-Diameter 1-20mm
- Micro Carbide Drill Bits 5D-Diameter 1-20mm
- Micro Carbide Drill Bits 8D-Diameter 3-20mm
8D Micro Diameter Drill Bits are eight times their diameter, designed for deep hole drilling in applications such as aerospace components and micro-hole assemblies in medical devices.
Corresponding table of processing range
Corresponding table of processing range |
|||||||||||||||||||||||||||||
P (Steel Material) |
H (Hardened Material) |
M (Stainless Steel) |
S (High Temperature Alloys and Titanium Alloys) |
K (Cast Iron) |
N (non-ferrous metals) |
||||||||||||||||||||||||
P1 |
P2 |
P4 |
P5 |
P6 |
P11 |
H3 |
H5 |
H7 |
H8 |
H12 |
H21 |
M1 |
M2 |
M4 |
S1 |
S2 |
S3 |
S11 |
K1 |
K2 |
K3 |
K4 |
N1 |
N2 |
N3 |
N4 |
N5 |
N10 |
N11 |
● |
● |
● |
|
○ |
|
○ |
|
○ |
|
○ |
○ |
○ |
|
|
|
|
● |
● |
● |
● |
|
|
|
|
|
|
|
||
● |
● |
● |
● |
|
○ |
|
○ |
|
|
○ |
|
○ |
○ |
○ |
|
|
|
|
● |
● |
● |
● |
|
|
|
|
|
|
|
● |
● |
● |
● |
|
○ |
|
○ |
|
|
○ |
|
○ |
○ |
○ |
|
|
|
|
● |
● |
● |
● |
|
|
|
|
|
|
|
● |
● |
● |
● |
|
○ |
|
○ |
|
|
○ |
|
○ |
○ |
○ |
|
|
|
|
● |
● |
● |
● |
|
|
|
|
|
|
|
● |
● |
● |
● |
|
○ |
|
○ |
|
|
○ |
|
○ |
○ |
○ |
|
|
|
|
● |
● |
● |
● |
|
|
|
|
|
○ |
○ |
● |
● |
● |
● |
|
○ |
|
○ |
|
|
○ |
|
○ |
○ |
○ |
|
|
|
|
● |
● |
● |
● |
|
|
|
|
|
○ |
○ |
● |
● |
● |
● |
|
○ |
|
○ |
|
|
○ |
|
○ |
○ |
○ |
|
|
|
|
● |
● |
● |
● |
|
|
|
|
|
○ |
○ |
● |
● |
● |
● |
|
○ |
|
○ |
|
|
○ |
|
○ |
○ |
○ |
|
|
|
|
● |
● |
● |
● |
|
|
|
|
|
○ |
○ |
○ |
○ |
|
|
|
○ |
|
|
|
|
○ |
|
● |
● |
● |
● |
● |
● |
● |
|
|
|
|
|
|
|
|
|
○ |
○ |
○ |
○ |
|
|
|
○ |
|
|
|
|
○ |
|
● |
● |
● |
● |
● |
● |
● |
|
|
|
|
|
|
|
|
|
○ |
○ |
○ |
○ |
● |
● |
● |
● |
|
● |
|
|
|
|
|
|
|
|
|
|
|
● |
● |
● |
● |
|
|
○ |
○ |
○ |
|
|
○ |
○ |
● |
● |
● |
● |
|
● |
|
|
|
|
|
|
|
|
|
|
|
● |
● |
● |
● |
|
|
○ |
○ |
○ |
|
|
○ |
○ |
● |
● |
● |
● |
|
● |
|
|
|
|
|
|
|
|
|
|
|
● |
● |
● |
● |
|
|
○ |
○ |
○ |
|
|
○ |
○ |
● |
● |
● |
● |
|
● |
|
|
|
|
|
|
|
|
|
|
|
● |
● |
● |
● |
|
|
○ |
○ |
○ |
|
|
○ |
○ |
● |
● |
● |
● |
|
● |
|
|
|
|
|
|
|
|
|
|
|
● |
● |
● |
● |
|
|
○ |
○ |
○ |
|
|
○ |
○ |
● |
● |
● |
● |
|
● |
|
|
|
|
|
|
|
|
|
|
|
● |
● |
● |
● |
|
|
○ |
○ |
○ |
|
|
- Most Adaptable
- Adapt
Corresponding table of processing range | |||||||||||||||||||||||||||||
P (Steel Material) | H (Hardened Material) | M (Stainless Steel) | S (High Temperature Alloys and Titanium Alloys) | K (Cast Iron) | N (Non-Ferrous Metals) | ||||||||||||||||||||||||
P1 | P2 | P4 | P5 | P6 | P11 | H3 | H5 | H7 | H8 | H12 | H21 | M1 | M2 | M4 | S1 | S2 | S3 | S11 | K1 | K2 | K3 | K4 | N1 | N2 | N3 | N4 | N5 | N10 | N11 |
● | ● | ● | ● | ● | ○ |
| ○ |
|
| ○ |
| ○ | ○ | ○ |
|
|
|
| ● | ● | ● | ● | ○ | ○ | ○ | ○ | ○ | ○ | ○ |
● | ● | ● | ● | ● | ○ |
| ○ |
|
| ○ |
| ○ | ○ | ○ |
|
|
|
| ● | ● | ● | ● | ○ | ○ | ○ | ○ | ○ | ○ | ○ |
● | ● | ● | ● | ● | ○ |
| ○ |
|
| ○ |
| ○ | ○ | ○ |
|
|
|
| ● | ● | ● | ● | ○ | ○ | ○ | ○ | ○ | ○ | ○ |
● | ● | ● | ● | ● | ○ |
| ○ |
|
| ○ |
| ○ | ○ | ○ |
|
|
|
| ● | ● | ● | ● | ○ | ○ | ○ | ○ | ○ | ○ | ○ |
● | ● | ● | ● | ● | ○ |
| ○ |
|
| ○ |
| ○ | ○ | ○ |
|
|
|
| ● | ● | ● | ● | ○ | ○ | ○ | ○ | ○ | ○ | ○ |
|
|
|
|
|
|
|
|
|
|
|
|
|
|
|
|
|
|
|
|
|
|
| ● | ● | ● | ● | ● | ● |
|
|
|
|
|
|
|
|
|
|
|
|
|
|
|
|
|
|
|
|
|
|
|
| ● | ● | ● | ● | ● | ● |
|
● | ● | ● | ● | ● | ○ |
| ○ |
|
|
|
|
|
|
|
|
|
|
| ● | ● | ● | ● |
|
|
|
|
|
|
|
|
|
|
|
|
|
|
|
|
|
|
|
|
|
|
|
|
|
| ● | ● | ● | ● | ● | ● | ● | ● | ● | ● |
|
|
|
|
|
|
|
|
|
|
|
|
|
|
|
|
|
|
|
| ● | ● | ● | ● | ● | ● | ● | ● | ● | ● |
|
● | ● | ● | ● | ● | ● | ● | ● | ● | ● | ● | ● | ● | ● | ● | ○ | ○ | ○ | ○ | ● | ● | ● | ● | ● | ● | ● | ● | ● | ● | ● |
● | ● | ● | ● | ● | ● | ● | ● | ● | ● | ● | ● | ● | ● | ● | ○ | ○ | ○ | ○ | ● | ● | ● | ● | ● | ● | ● | ● | ● | ● |
|
- Most Adaptable
- Adapt
Hole Cutting Tools
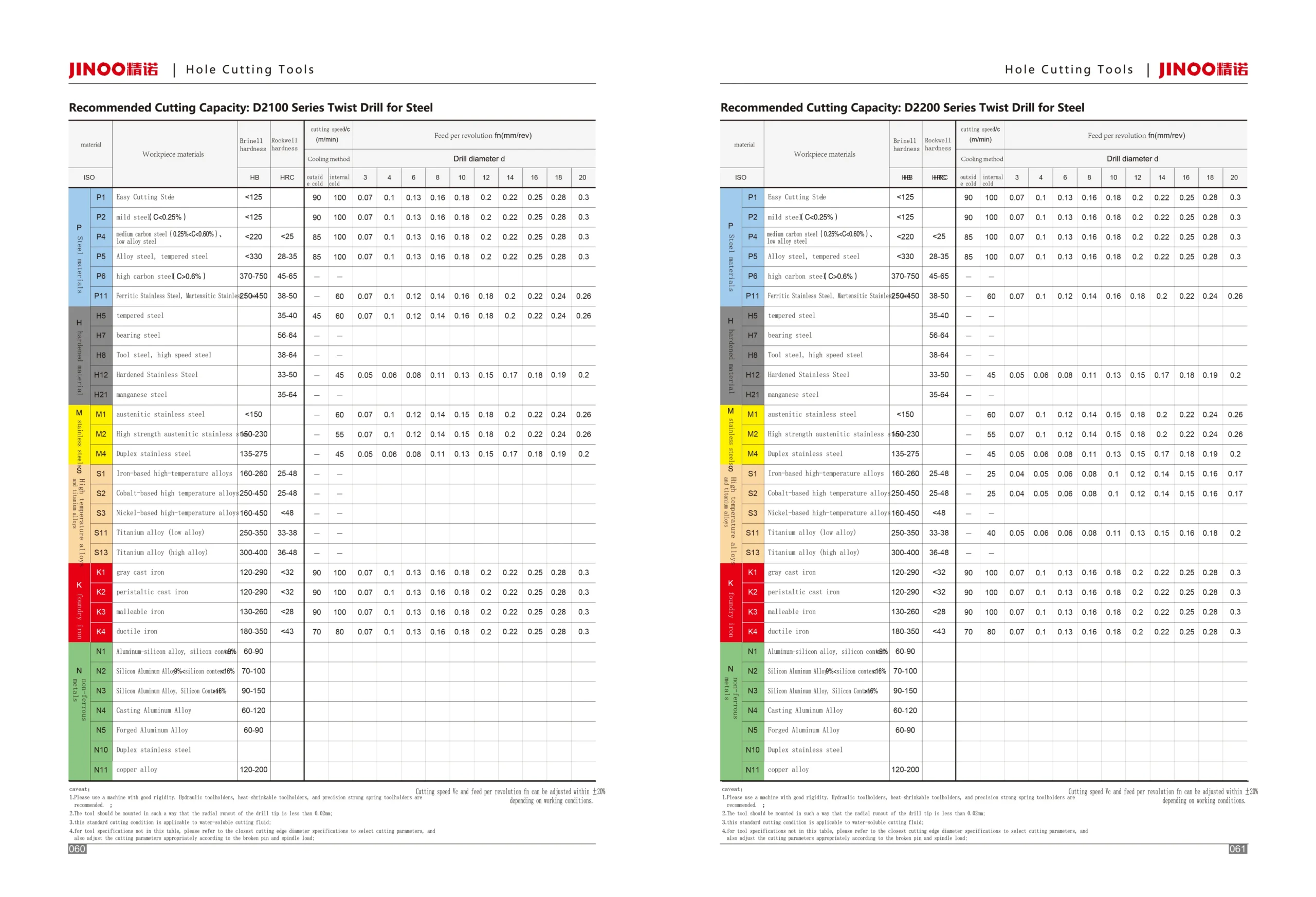
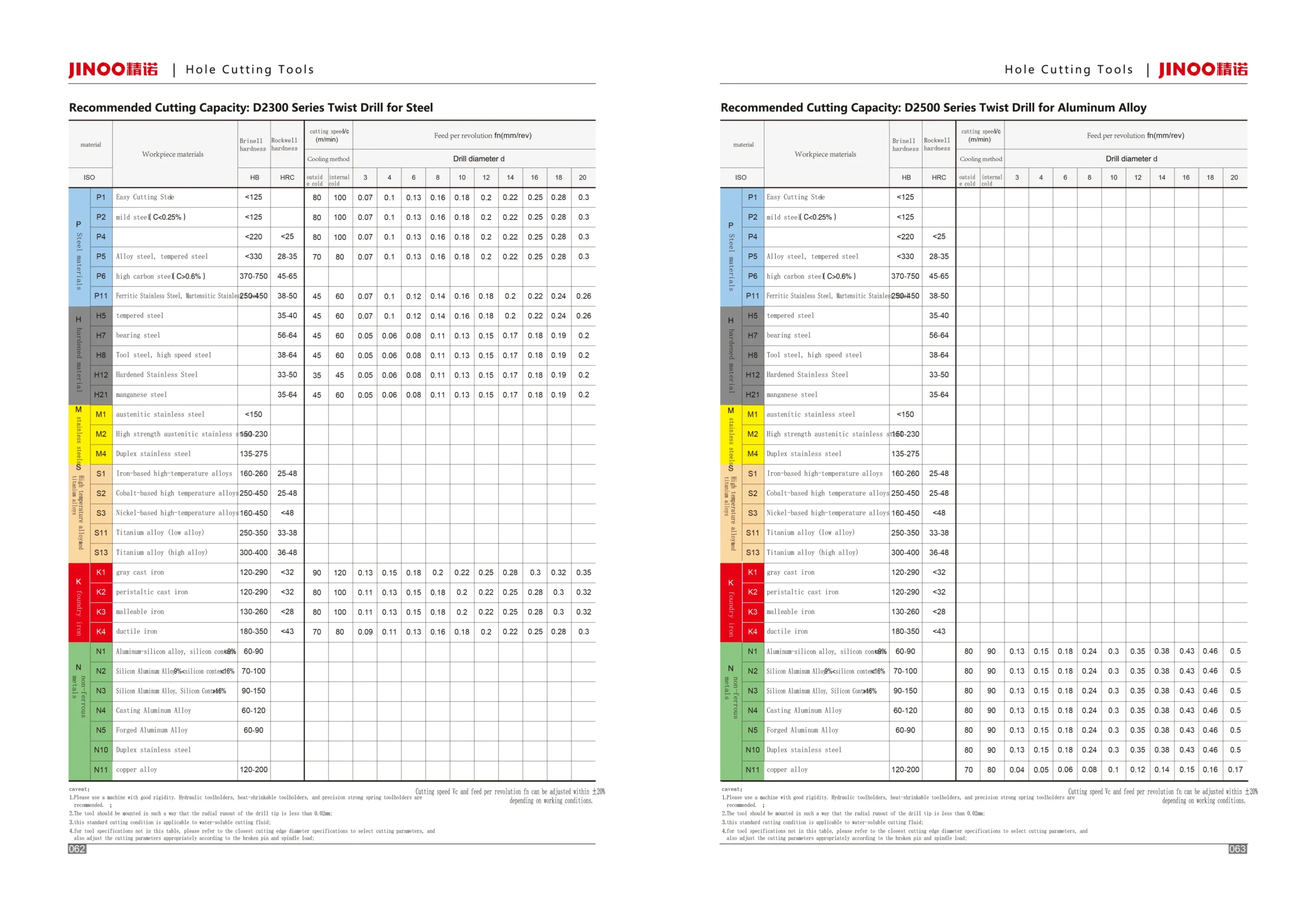
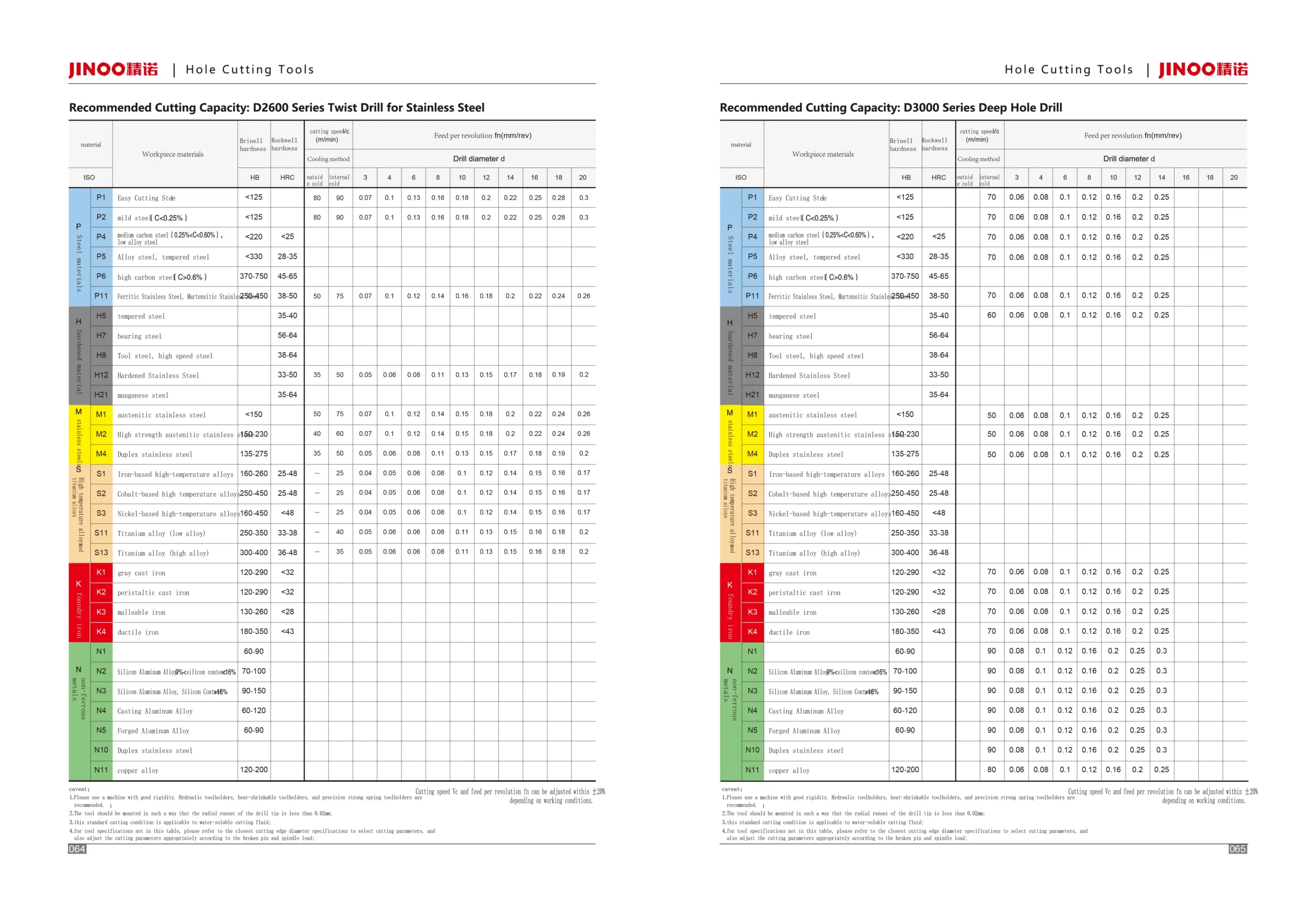
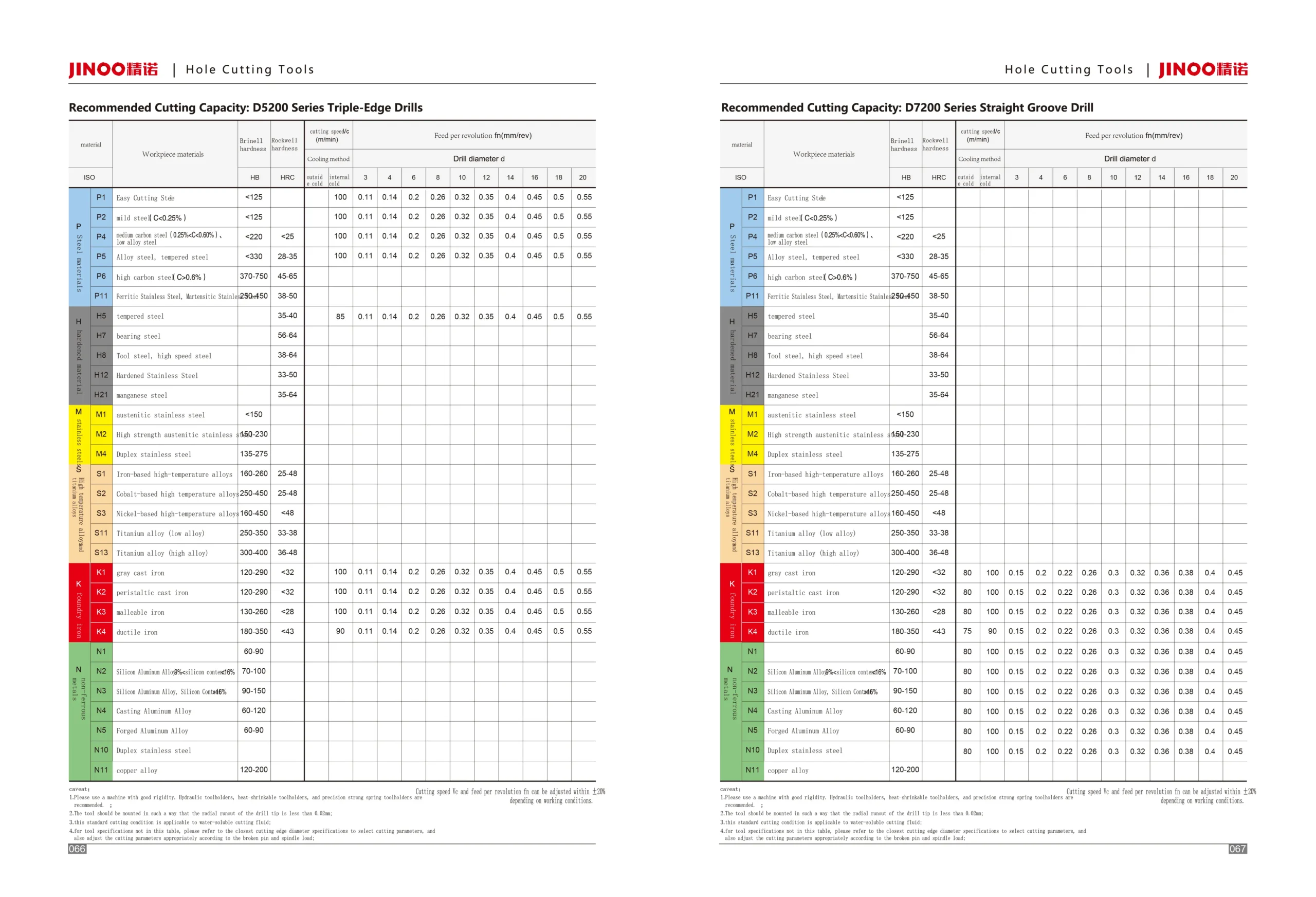
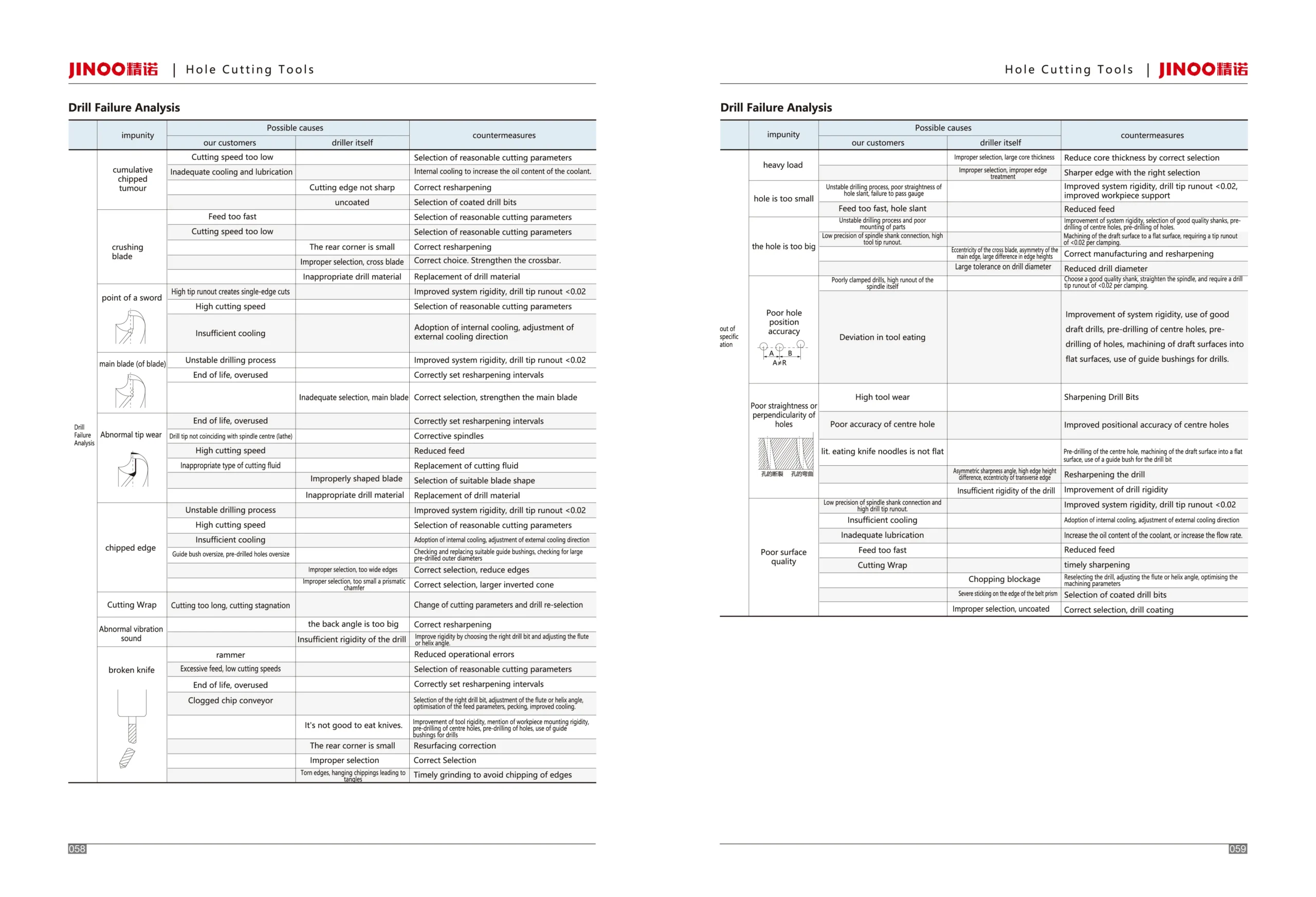
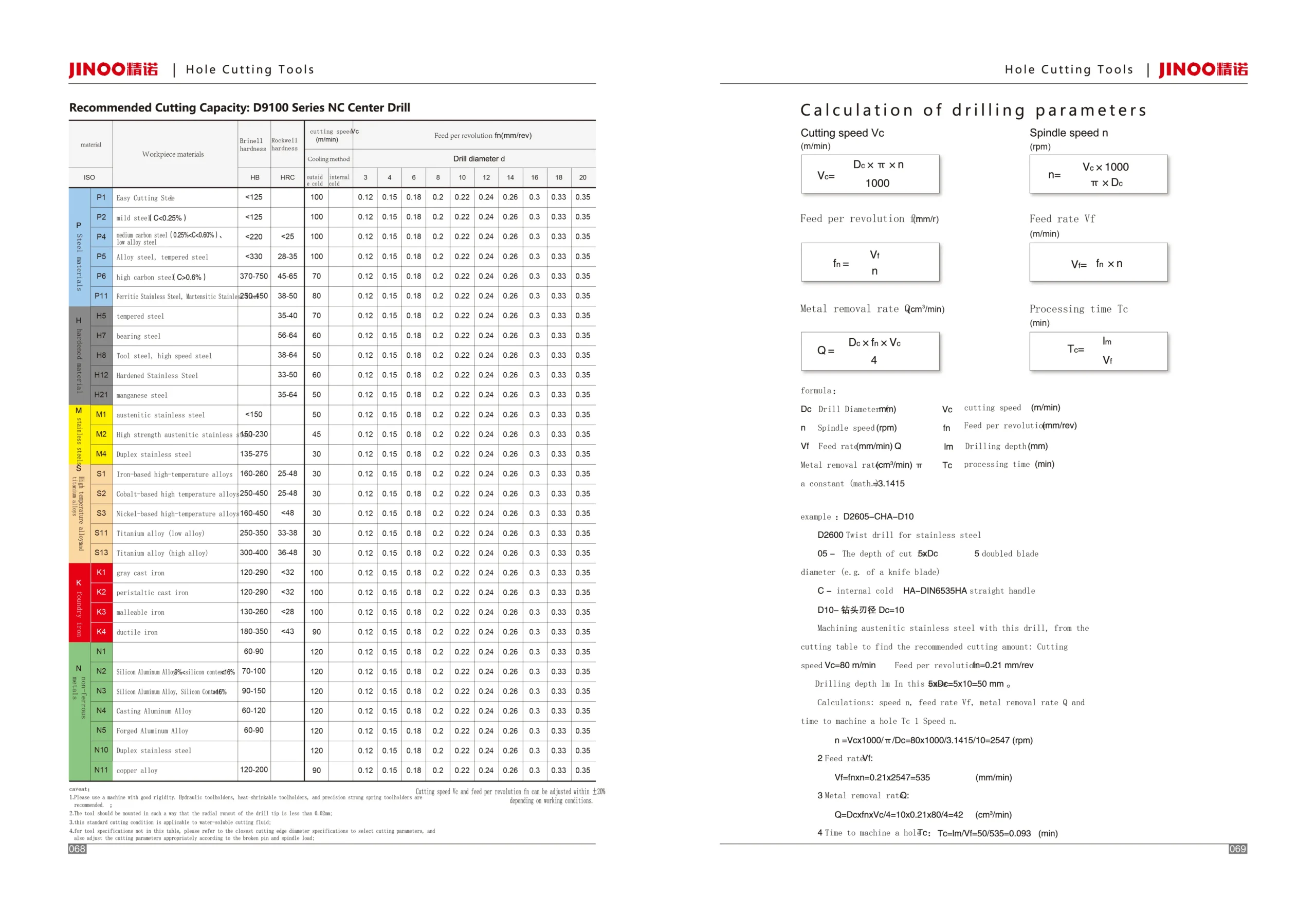
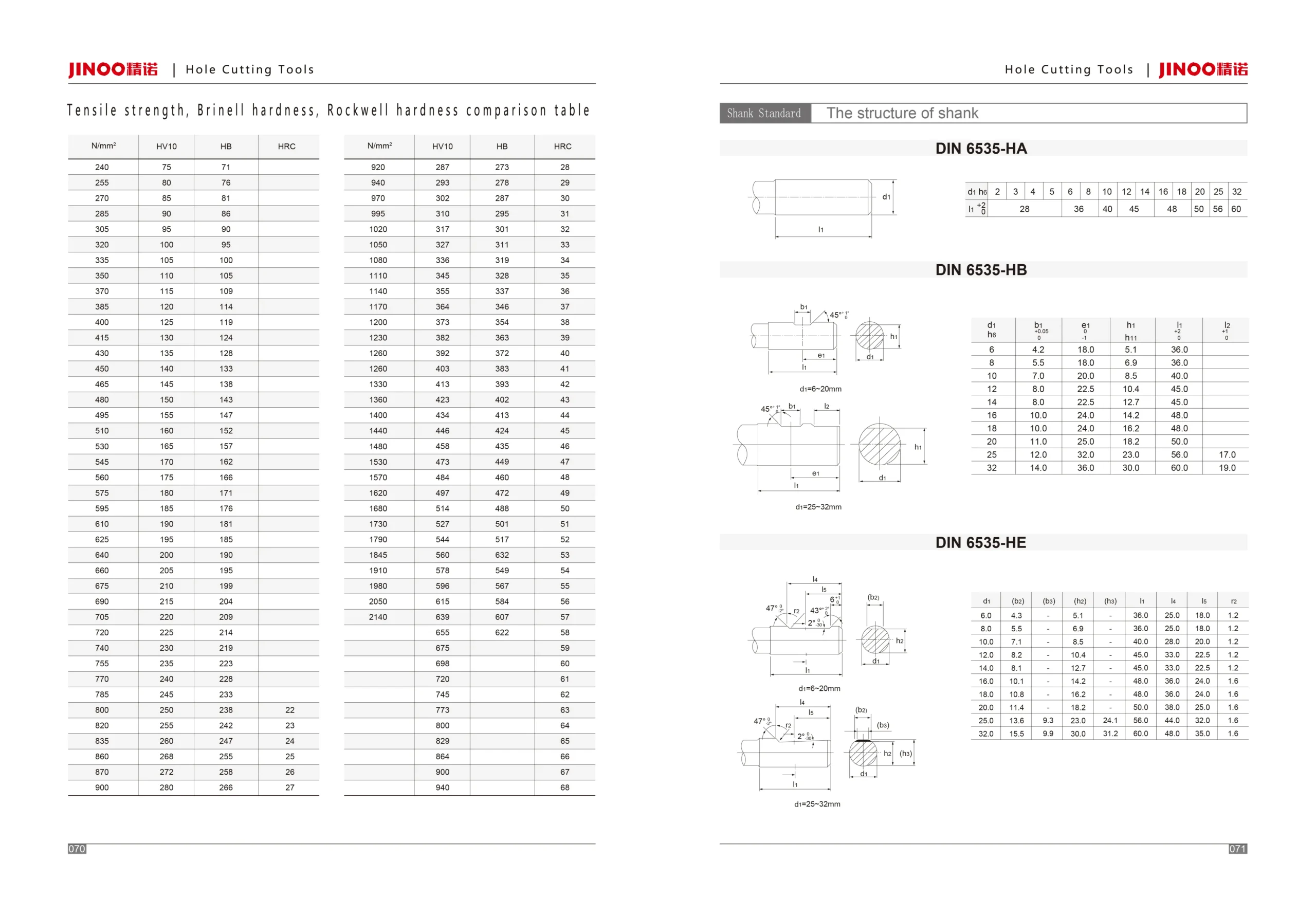
Drill Coding Rules:
D | 26 | 05 | – | C | HA | – | 0800 | ||||||
⑴ | ⑵ | ⑶ |
| ⑷ | ⑸ |
| ⑹ | ||||||
⑴ | – | Product Category |
| D | Drill Bits | ||||||||
⑵ | – | Product Series |
| 21 | Twist drills for steel | ||||||||
| 22 | Twist drills for steel | |||||||||||
23 | Twist drills for steel | ||||||||||||
25 | Twist drills for aluminium | ||||||||||||
26 | Twist drills for stainless steel | ||||||||||||
30 | Deep Hole Twist Drills | ||||||||||||
52 | Three-flute drills | ||||||||||||
72 | Straight Groove Drill | ||||||||||||
91 | NC Centre Drill | ||||||||||||
⑶ | – | Depth of Cut |
| 00 | Centre Drill | ||||||||
| 03 | 3xd | |||||||||||
05 | 5xd | ||||||||||||
08 | 8xd | ||||||||||||
20 | 20xd | ||||||||||||
⑷ | – | Cooling Method |
| N | External Coolant | ||||||||
| C | Internal Coolant | |||||||||||
⑸ | – | Shank Form |
| HA | DIN6535HA | ||||||||
| HB | DIN6535HB | |||||||||||
HE | DIN6535HE | ||||||||||||
YZ | Plain Cylindrical Shank | ||||||||||||
⑹ | – | Blade Diameter |
| 0050 | 0.5mm | ||||||||
| 0100 | 1mm | |||||||||||
0800 | 8mm | ||||||||||||
1000 | 10mm |
Workpiece Material Table:
Material Group ISO |
Workpiece Materials |
Quantity Contained |
Tensile Strength |
Brinell Hardness |
Rockwell Hardness | |
|
| N / m m 2 | HB | HRC | ||
P Material of Steel Parts | P1 | Easy Cutting Steels |
| < 320 | < 125 |
|
P2 | Low Carbon Steel | C < 0.25% | 320-530 | < 125 |
| |
P4 | Medium Carbon Steels, Low Alloy Steels | 0.25% < C < 0.60% | 520-850 | < 220 | < 25 | |
P5 | Alloy Steel, Tempered Steel |
| 550-1200 | < 330 | 28-35 | |
P6 | High Carbon Steel | C > 0.6% | 600-1200 | 370-750 | 45-65 | |
P11 | Ferritic Stainless Steel, Martensitic Stainless Steel |
| 600-1350 | 250-450 | 38-50 | |
H Hardened Material | H3 | Surface Hardened Steel |
| 800-1500 |
| 58-62 |
H5 | Tempered Steel |
| 490-1200 |
| 35-56 | |
H7 | Bearing Steel |
| 900-1600 |
| 56-64 | |
H8 | Tool Steels, High Speed Steels |
|
|
| 60-64 | |
H12 | Hardened Stainless Steels |
|
|
| 33-50 | |
H21 | Manganese Steels |
|
|
| 35-64 | |
M Stainless Steels | M1 | Austenitic Stainless Steel |
| 600-1100 | < 150 |
|
M2 | High Strength Austenitic Stainless Steels |
| 1100-1750 | 150-230 |
| |
M4 | Duplex Stainless Steels |
| 600-1300 | 230-310 |
| |
S High Temperature Alloys and Titanium Alloys | S1 | Iron-Based High Temperature Alloys |
| 500-1200 | 160-260 | 25-48 |
S2 | Cobalt-Based High Temperature Alloys |
| 1000-1450 | 250-450 | 25-48 | |
S3 | Nickel-Based High Temperature Alloys |
| 600-1700 | 160-450 | < 48 | |
S11 | Titanium Alloys |
| 900-1600 | 300-400 | 33-38 | |
K Foundry Iron | K1 | Grey Cast Iron |
| 130-340 | 110-270 | < 32 |
K2 | Peristaltic Cast Iron |
| 300-570 | 120-290 | < 32 | |
K3 | Malleable Iron |
| 200-530 | 150-290 | < 28 | |
K4 | Ductile Cast Iron |
| 400-900 | 180-350 | < 43 | |
N Non-Ferrous Metals (All Metals Excluding Iron, Chromium, Manganeseand their Alloys) | N1 | Aluminium-Silicon Alloys | Silicon Content <9 Percent | < 200 | 60-90 |
|
N2 | Silicon Aluminium Alloys | 9%<Silicon Content<16% | 200-300 | 70-100 |
| |
N3 | High Silicon Aluminium Alloys | Silicon Content >16 Percent | 200-350 | 90-150 |
| |
N4 | Casting Aluminium Alloy |
| 155-460 | 45-100 |
| |
N5 | Forged Aluminium Alloys |
|
| 60-90 |
| |
N10 | Copper |
| 20-30 | 35-45 |
| |
N11 | Copper Alloy |
|
| 120-200 |
|