Die-Mold
“”JINOO CNC tools are used to precisely machine molds and dies with complex shapes and tight tolerances. They enable manufacturers to create detailed and accurate molds for processes like injection molding, casting, and stamping, resulting in high-quality and consistent parts production.”
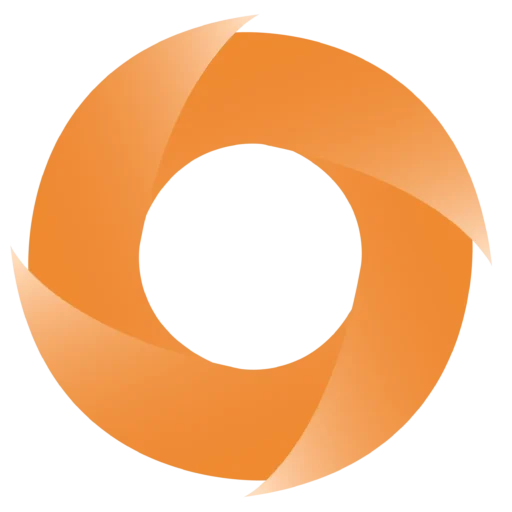
JINOO 精诺
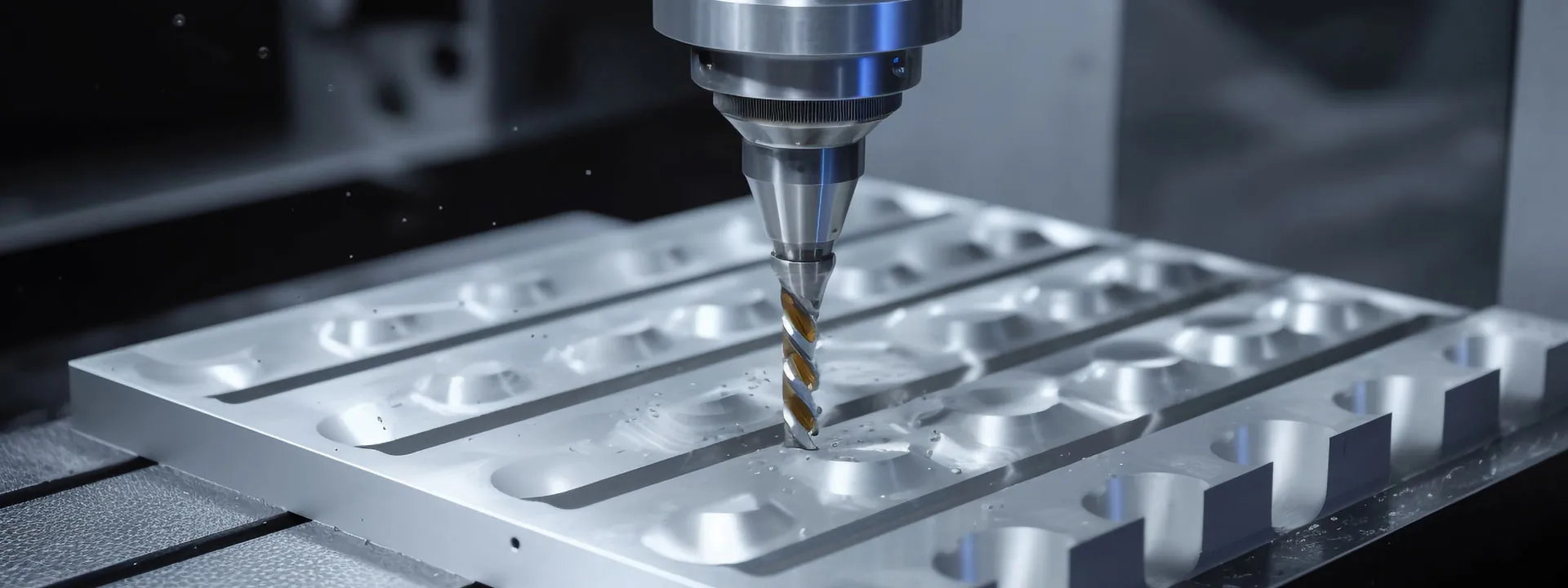
Application Scenarios
Abrasive manufacturing:
1.Mould processing: processing of abrasive mould parts to ensure shape accuracy and dimensional stability.
2.Substrate processing: Processing the positioning holes and mounting holes of the abrasive substrate to ensure accurate installation.
3.Abrasive embedding: Processing of slots and holes for abrasive embedding to ensure that the abrasive is firmly fixed.
Manufacturing of abrasive equipment:
1.Processing of equipment parts: Processing of key parts of grinding machines, sanders and other equipment to ensure stable operation.
2.Precision hole machining: Machining precision holes in equipment to ensure performance and longevity.
Abrasive repair and maintenance:
1.Dimensional correction: Repairing worn parts by milling and reaming to extend the life of grinding tools.
2.Hole Adjustment: Repair mounting and positioning holes to ensure proper installation.
Advantages
High hardness and wear resistance:
- Suitable for high hardness material machining: effectively machining alloy steel, cemented carbide, etc., avoiding rapid tool wear.
- Extend tool life: reduce wear and tear, reduce replacement frequency, improve efficiency.
High temperature resistance and stability:
- High temperature resistance: maintain high hardness and cutting performance in high temperature machining.
- Stable cutting performance: ensure consistent machining quality.
High Precision and Quality Surface:
- Achieve high-precision machining: meet strict requirements for dimensions and tolerances.
- Enhance surface finish: Improve the surface quality of grinding tools and enhance the grinding effect.
Adapting to Complex Machining Needs:
- Processing complex shapes: Efficiently handle complex contours and deep cavities.
- Multi-material compatibility: Suitable for processing a wide range of materials.
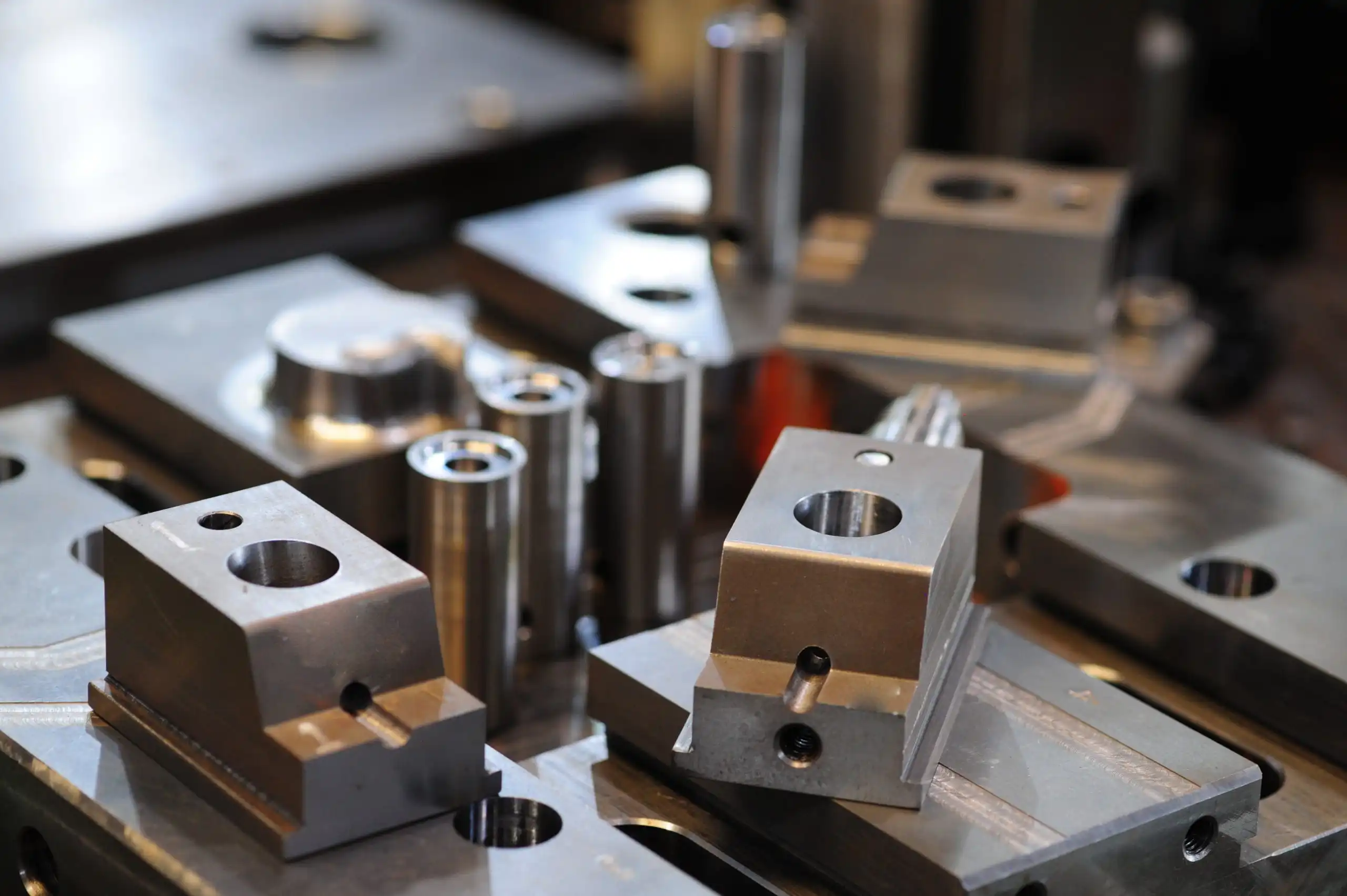
Industry convenience
- High-efficiency machining: shorten the machining cycle to meet the production demand.
- Reduce tool costs: extend tool life and reduce the number of replacements.
- High consistency: ensure consistent product quality and reduce dimensional deviation.
- Conform to strict standards: meet high precision and high reliability requirements.
- Adapt to automated production: support unmanned and intelligent manufacturing.
- Meet new material processing: effectively process new high hardness materials.
- Dry cutting: Reduce the use of cutting fluid and reduce environmental pollution.
- Improve material utilisation: reduce scrap rate and save resources.