Aerospace
“In aerospace applications, JINOO advanced CNC machining tools deliver precision and reliability, ensuring products meet the stringent aviation standards required for commercial, defense, and exploration purposes.”
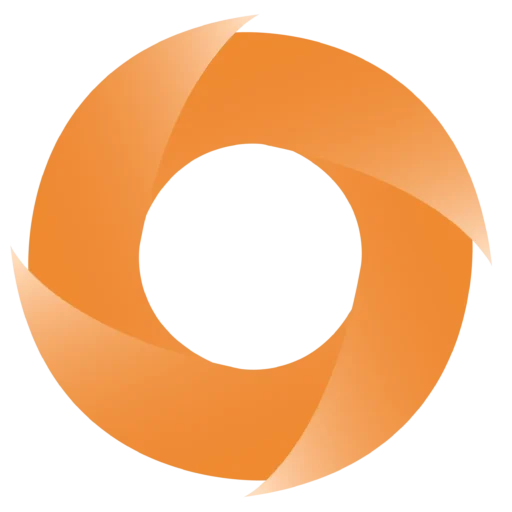
JINOO 精诺
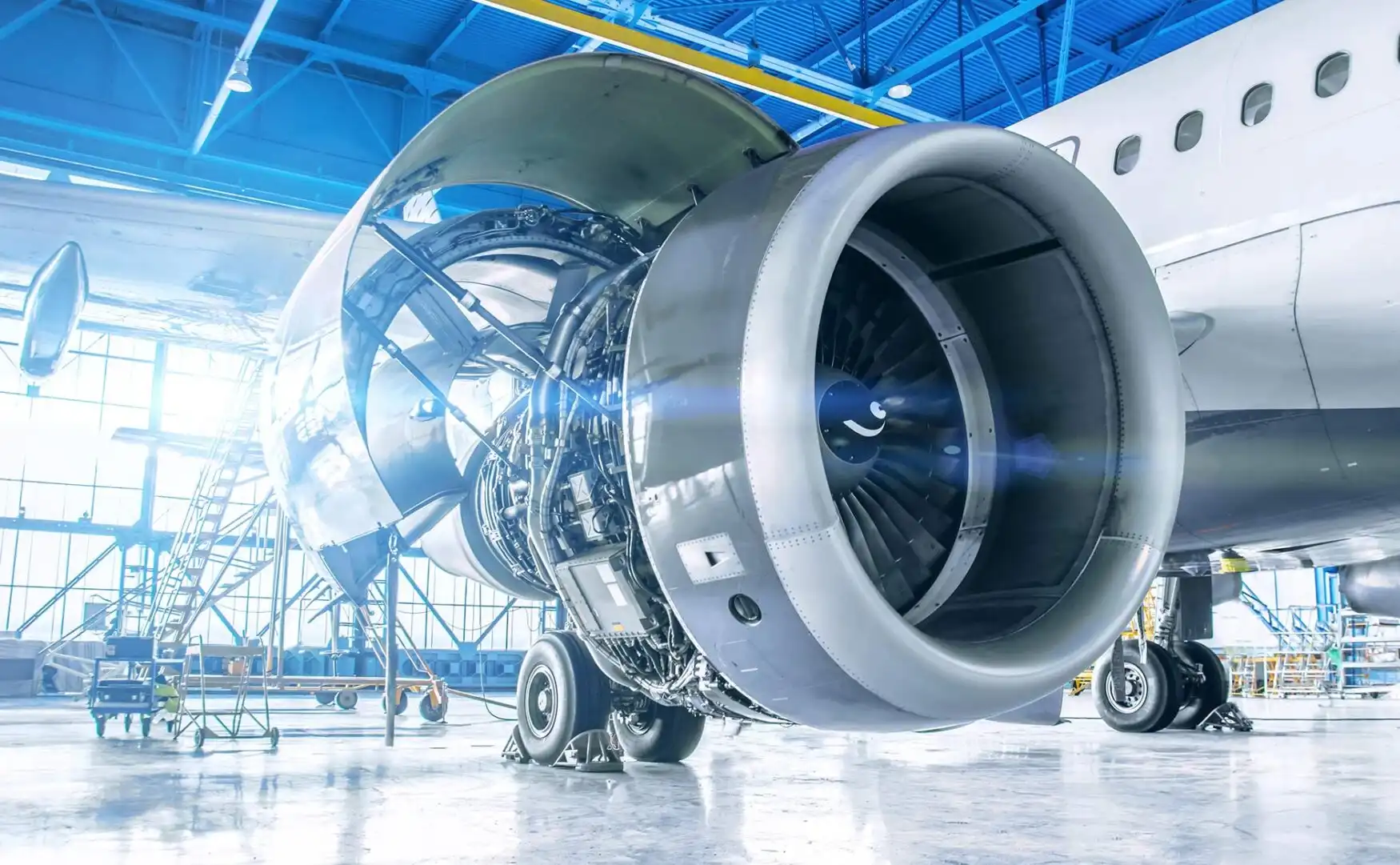
JINOO's Carbide Drill Bits
JINOO’s Carbide Drill Bits:
Used for drilling of high strength, difficult-to-machine materials (e.g. titanium alloys, nickel-based alloys, stainless steel, composite materials). Include:
- Aircraft structural parts: machining connection holes in key parts such as wings and fuselage, requiring high precision and high reliability.
- Engine components: drilling cooling holes in turbine blades, combustion chambers, which need to withstand high temperature and high pressure environments.
- Spacecraft components: processing precision holes in satellite and rocket components, requiring extremely high dimensional accuracy and surface quality.
JINOO's Cemented Carbide End Mills
Used for milling of complex curved surfaces and high-precision parts, applications:
- Aircraft structural parts: machining the shape and internal structure of aluminium alloy or titanium alloy structural parts.
- Engine parts: machining complex surfaces and grooves of turbine discs and blades.
- Composite parts: milling carbon fibre, glass fibre, etc. to prevent delamination and burrs.
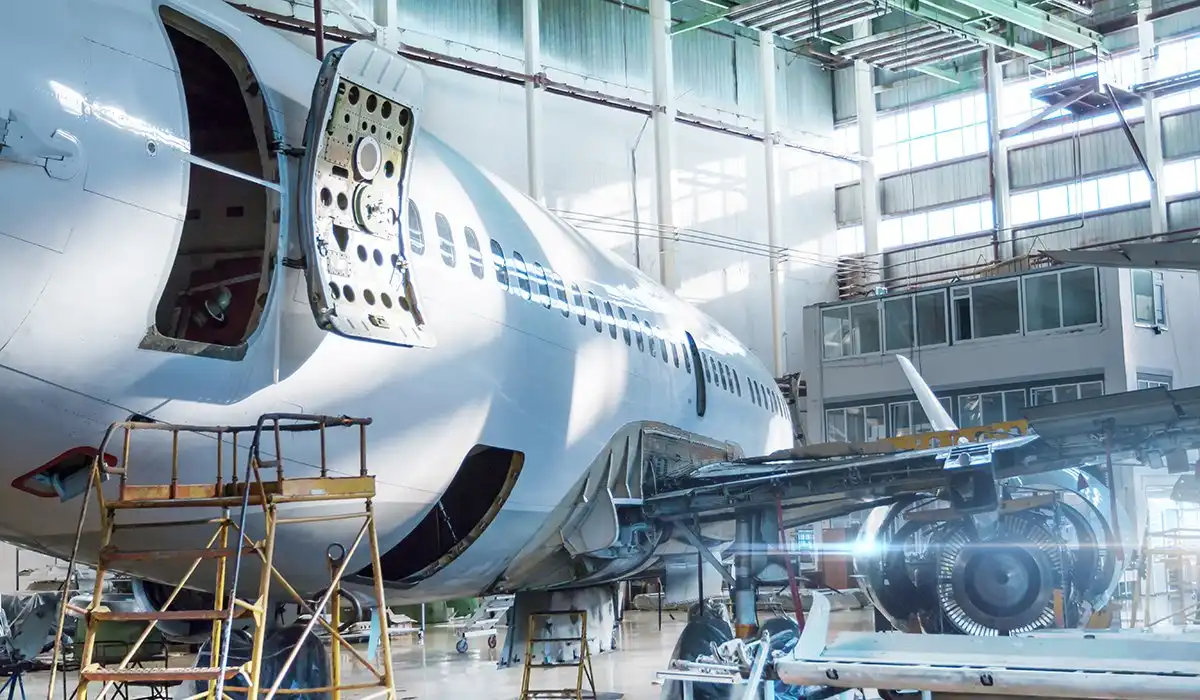
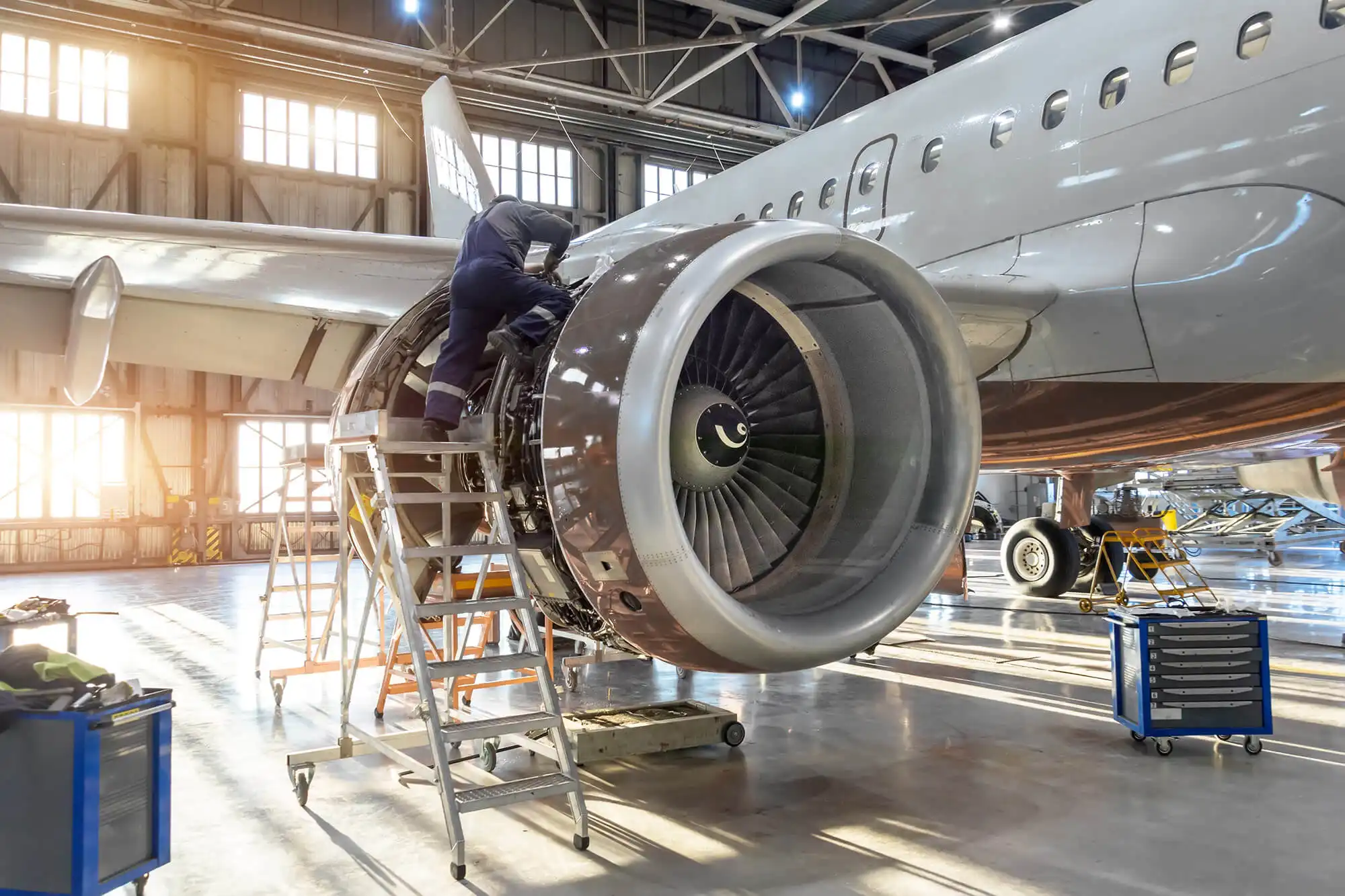
JINOO’s Carbide Reamer
Used for finishing high-precision holes to ensure that the hole diameter and surface quality meet strict requirements:
- Precision assembly holes: machining positioning holes for aircraft and engine components to ensure assembly accuracy.
- Hydraulic and fuel systems: machining precision holes for valve and pump bodies, requiring high finish.
- Aerospace instrumentation holes: holes for navigation equipment, requiring high reliability and long life.
Advantages
High hardness and wear resistance: suitable for machining high-strength materials, prolonging tool life and reducing replacement frequency.
High temperature resistance and stability: stable performance in high temperature and high speed cutting to meet the high requirements of the industry.
High precision and high quality surface: achieve micron-level machining accuracy, improve the fatigue strength and life of parts.
Adaptation to complex machining: Highly efficient machining of complex curved surfaces and shaped structures, applicable to a wide range of materials.
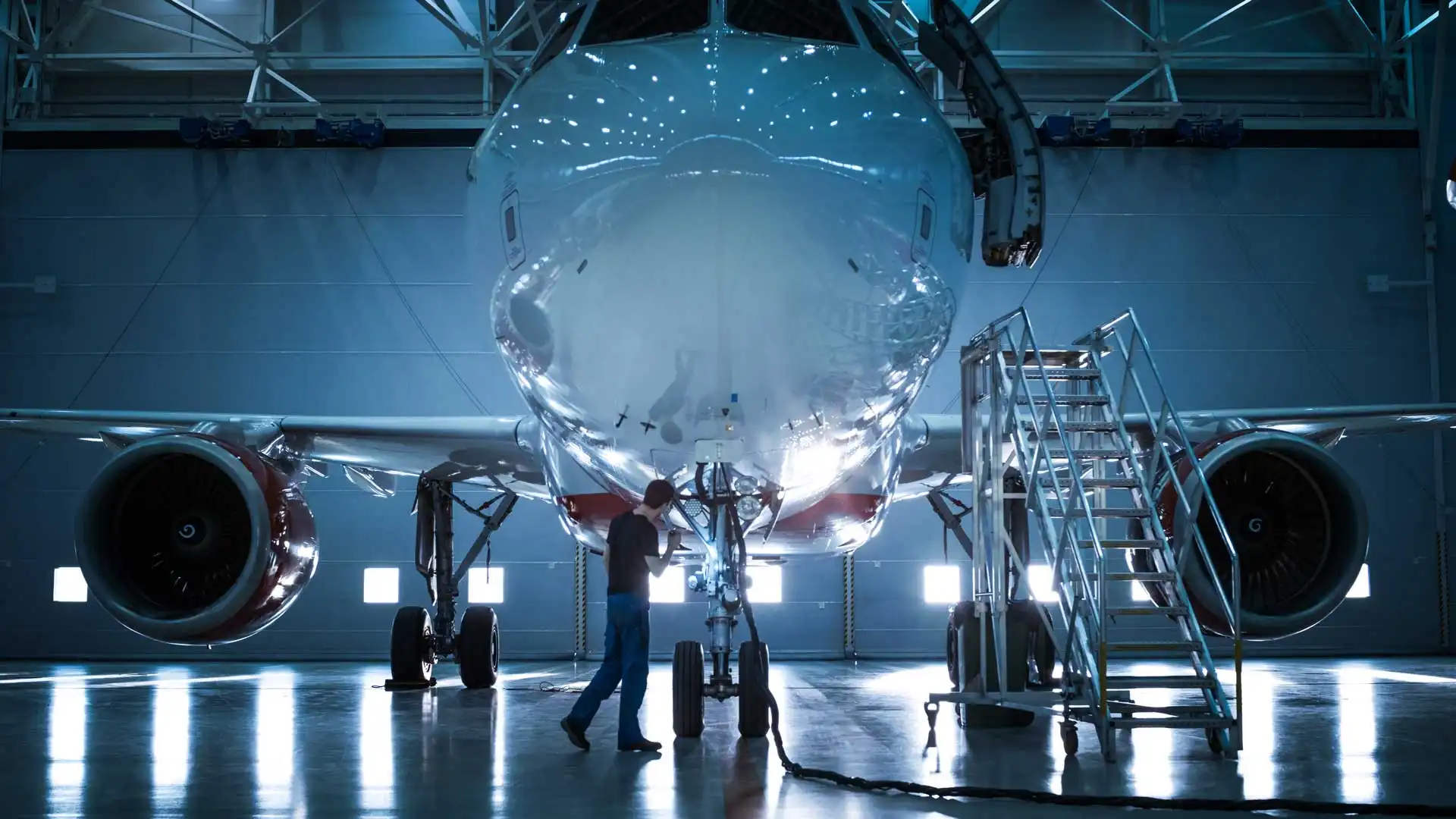
Industry convenience
Allow higher cutting speeds, shorten machining cycles and reduce costs.
Stable cutting performance ensures consistent part quality and meets stringent standards.
Suitable for high-speed machining and 5-axis machine tools to meet the needs of new material processing.
Suitable for dry or micro-lubricated cutting, reducing environmental pollution and improving material utilisation.