3C
“In the 3C industry (Computer, Communication, and Consumer electronics), CNC tools are used to precisely machine components like smartphone frames, laptop housings, and small electronic parts. They enable the production of intricate designs with tight tolerances, ensuring high-quality, consistent parts made from materials like aluminum and specialized plastics.“
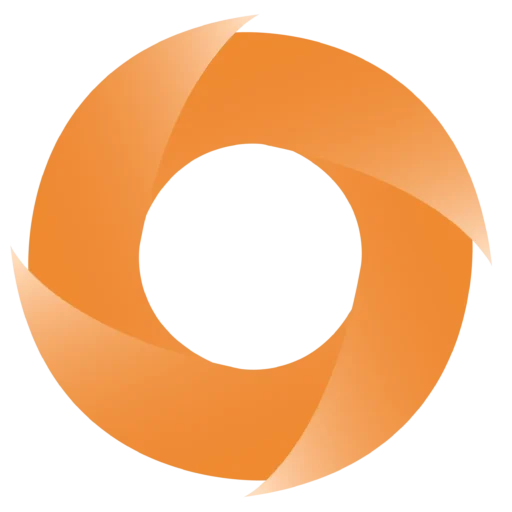
JINOO 精诺
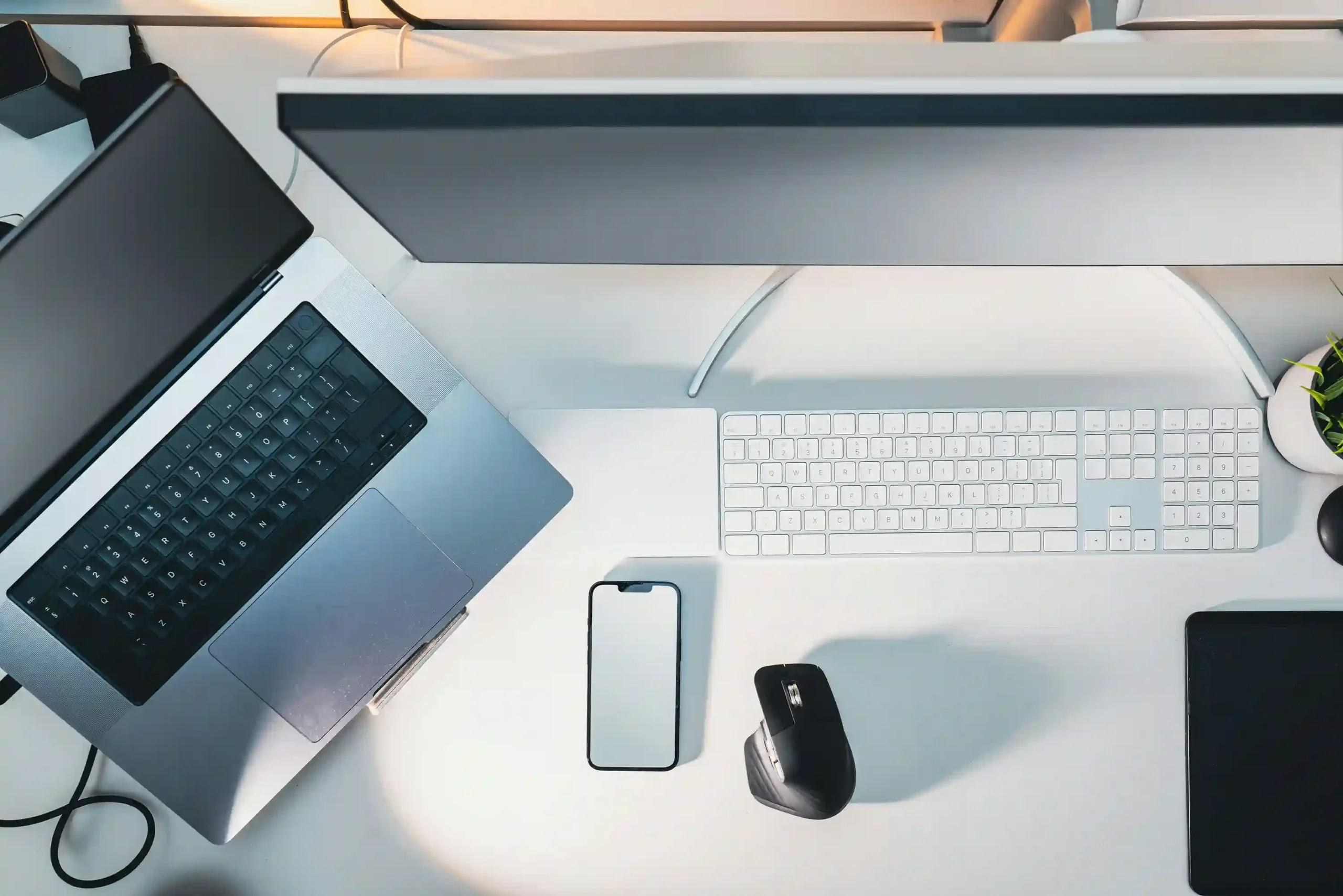
Application Scenarios
Manufacturing of mobile phones and tablet devices:
1.Shell machining: for machining holes, slots and contours of metal shells for mobile phones and tablet PCs, materials include aluminium alloy, magnesium alloy, stainless steel, etc.
2.Internal structural components: Machining of positioning holes, threaded holes and heat dissipation grooves of internal components to ensure precise assembly and heat dissipation performance.
Laptop and Accessory Manufacturing:
1.Chassis and frames: Milling of chassis and frames for laptop computers to meet the demand for thinness and high strength.
2.Interface parts: drilling and reaming of precision holes for USB and audio interfaces to ensure stable and reliable signal transmission.
Wearable Device Manufacturing:
1.Processing of exterior parts: Processing of complex curved surfaces and tiny structures of smartwatches, bracelets, etc., in materials such as titanium alloy and medical stainless steel.
2.Functional parts: machining sensor mounting holes, button holes and micro threaded holes, which require extremely high precision and surface quality.
Advantage
High precision and quality surface:
1.Micron-level machining: Achieve micron-level precision to meet the strict size and tolerance requirements of 3C products.
2.Enhanced Finish: Reduces the need for subsequent polishing and improves product appearance quality.
High hardness and wear resistance:
1.Processing high hardness materials: effectively process aluminium alloys, titanium alloys and stainless steel to extend tool life and improve efficiency.
2.Reduced wear: Maintains low wear rates in high-speed machining to ensure machining consistency.
High speed cutting performance:
1.Improve efficiency: withstand high cutting speeds and feeds, shorten machining cycles and meet the needs of mass production.
2.Adapt to high-speed equipment: performs well on high-speed CNC machine tools and machining centres, supporting automated production.
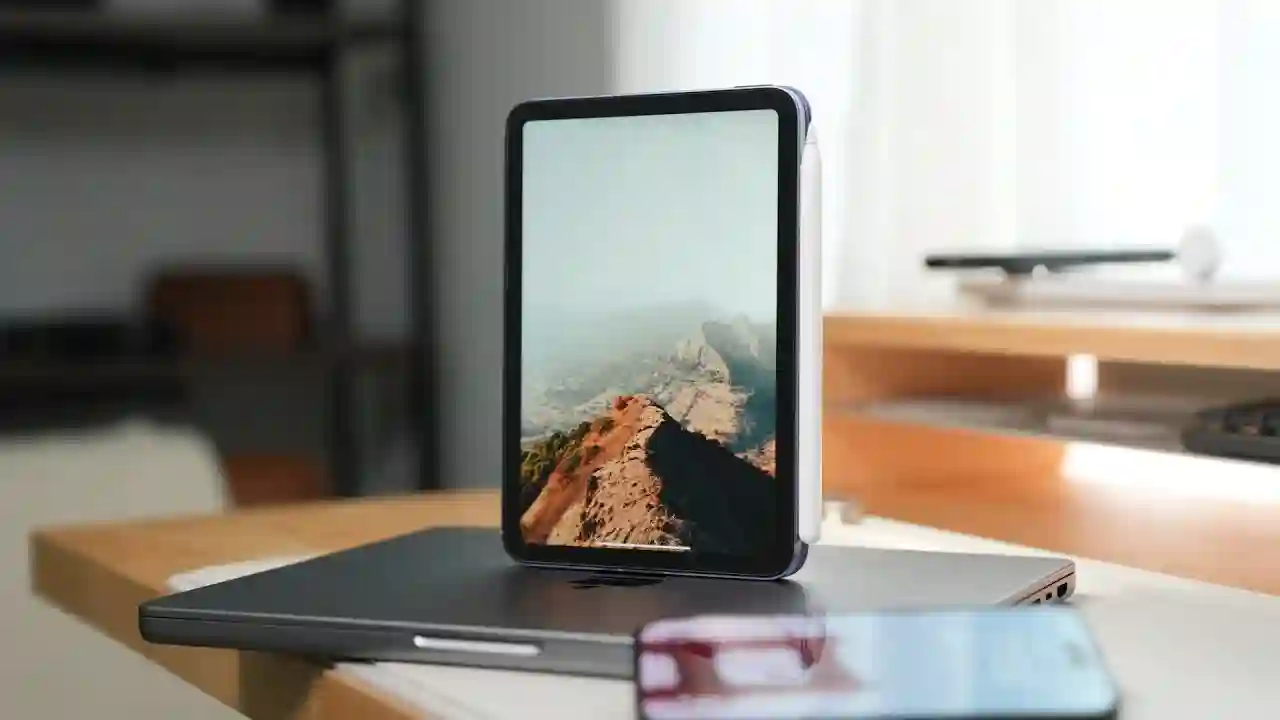
Industry convenience
- High-efficiency machining: shorten machining time to meet the market demand of fast time-to-market.
- Reduce tooling costs: Long tool life reduces replacement frequency and inventory costs.
- High Consistency: Stable cutting performance ensures consistent product quality and reduces reject rates.
- Meet stringent standards: meet the 3C industry's high-precision and high-reliability requirements to enhance product competitiveness.
- Compatible with automated equipment: suitable for high-speed machining centres, robotic machining cells, supporting unmanned production.
- Standardised management: Stable tool performance helps standardisation and data management of machining parameters.